Our frontline workers are fighting hard to deal with the COVID-19 pandemic crisis, and it has prompted everything else to take a backseat. Motorsports too in fact, is one of the worst hit because the usual race season has been suspended and races either cancelled or postponed. The 2019/20 season of Formula E has also been indefinitely suspended until things stabilise. This, however, has given us an opportunity to know more about what happens behind closed doors with the development of electric racing cars. As the electric vehicle segment expands its horizon as the future of mobility, we catch up with Mahindra Racing's battery partner Umicore to understand more about developing batteries for racing and the long-term sustainability of electric batteries in the times to come.
Also Read: Coronavirus Forces Extension Of 2019/20 Formula E Suspension
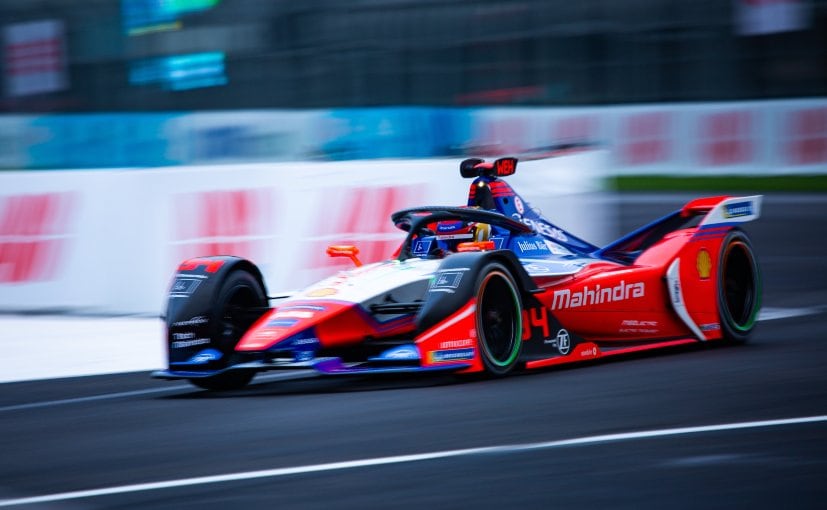
Mahindra Racing secured 28 points in the Mexico ePrix and are now gearing up for the Marrakesh ePrix this weekend
Mahindra Racing and Umicore entered into a partnership in 2017 and have been working together to develop compact and high-performance batteries for the world's first all-electric single-seater racing series. Umicore is a mobility materials and recycling company that has, in recent times, diverted its attention towards technology-focussed recycling of precious metals. With Mahindra Racing, the firm has been working on improving lithium-ion battery technology that helps the company optimise the production of active materials like cathode. With the high-octane atmosphere surrounding Formula E cars, the batteries undergo heavy wear and tear, and thus, are the perfect test bed for testing materials at Umicore.
Tom Van Bellinghen, VP OEM Value Chain & Marketing, Umicore Rechargeable Battery Materials says, "Umicore offers its battery materials knowhow to Mahindra Racing, one of the teams competing in the Formula E championship, and we close the battery loop by recycling the cells after their use in the racing cars. This 'closed loop' approach results in a dramatically lower environmental footprint of the resulting battery materials."
RACE TO ROAD
Motorsport has always been the real-time research and development centre for new car technologies. F1 paved the way for some of the most exciting sports cars, and Formula E is now helping shape the electric vehicle sector. Not just Mahindra, but Formula E now packs in a host of global manufacturers right from Nissan, Mercedes to Porsche and Audi. The latter VW Group companies have also given up on their endurance racing participation focussing synergies on electric racing and mobility. Battery technology then is the focal point of development in electric racing. There are, of course, the traction batteries that provides the power to the electric motor, while a smaller 12 volt auxiliary battery powers the other systems on the race car. This is where Umicore and Mahindra are working together.
The 12V auxiliary battery has been used on the Gen2 racing cars that hit the tracks in 2018. The battery powers the critical electrical systems including brake lights, radio communication, electronics and needs to be as light as possible to maximise weight savings. The auxiliary battery runs independently from the traction battery and needs to weigh a minimum to keep the overall weight savings in check. This auxiliary input lithium-ion battery helps Umicore understand the use active materials inside. The key materials can then be packed better, which further helps more sustainable batteries for road-going cars. It also allows for compact battery manufacturing with cathode production reduced from the gram scale to the hundreds of mT/m scale.
ETHICAL SOURCING OF RAW MATERIALS
With electric mobility gaining traction, there's always been the question if raw materials have been sourced ethically to meet the sudden spike in demand. The Belgian company says that it has a systems in place for labour and environmental practices in the supply chain. With respect to ethically sourcing of cobalt, Umicore says that the company has ' Sustainable Procurement Framework' that requires suppliers to adhere to specific standards for environmental stewardship, labour practices, human rights, business integrity and supply-chain management.
The supply of cobalt also comes from geographical risks that does put sourcing the active material a task from an ethical standpoint. It's all the more important to push recycling and re-use active materials from current batteries.
Also Read: Mahindra Racing's Pascal Wehrlein Wins Round 3 Of Race To Home Challenge
RE-USE AND RECYCLE
Umicore's recycling capabilities and practices allows the company to re-use active materials from existing batteries. However, given the current adoption of EVs, it will take a while before this generation of lithium-ion batteries reach their shelf life and are recycled for key materials.
Elaborating on the recycling process, Tom says, "In our current recycling process sustainability comes first, battery energy and the organic part of the battery materials are used in the smelting process as an energy carrier which thereby reduces the consumption of primary energy."
With Formula E, Umicore and the sport organisers have entered a partnership to recycle lithium-ion battery unit and cells that were used during the first two seasons of the series. These batteries are then broken down with the focus on recovering lithium, cobalt, nickel and copper. The smelting technology developed by Umicore helps recycle the materials into their purest form and to convert them into active cathode materials for the production of rechargeable batteries. The cells are reutilised and not crushed that would otherwise expose operators to hazardous compounds.
Batteries are the fuel of electric vehicles and it is this development cycle that will find its way on the cars and two-wheelers of the future. Formula E has been shaping the electric vehicle technology and the subsequent components around the cars. The technology does limit to more compact and complex manufacturing of batteries, but will also help develop shorting charging times, long usage period and higher performance. There's also heat management that will need to be packed in more efficiently as performance and range increase, going forward.
from CarandBike - Latest News https://ift.tt/3fUcbdY
0 Comments